Understand the principle, characteristics and application types of piezoresistive sensor
Release time: 2024-08-14
Piezoresistive sensor is a device made of diffusion resistance on the substrate of semiconductor material according to the pieozoresistive effect of semiconductor material. The substrate can be directly used as a measuring sensing element, and the diffusion resistance is connected into a bridge inside the substrate.
Pressure resistance typeSensor principle
Piezoresistance sensor piezoresistance type transducer refers to the sensor made of the piezoresistance effect of monocrystalline silicon material and integrated circuit technology. After the force of monocrystalline silicon material, the resistivity changes, and the electricity proportional to the force change can be obtained by measuring the circuitsignaloutput. Piezoresistive sensors are used for the measurement and control of pressure, tension, pressure difference, and other physical quantities that can be converted into force changes (like fluid level, acceleration, weight, strain, flow, vacuum).
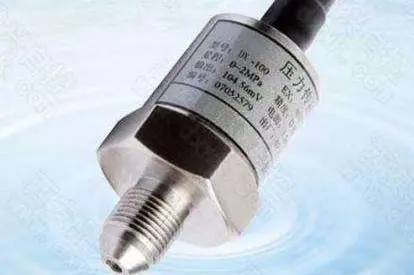
A piezoresistive sensor is a device made of diffusion resistance on the substrate of a semiconductor material according to the piezoresistive effect of a semiconductor material. The substrate can be directly used as a measuring sensing element, and the diffusion resistance is connected into a bridge inside the substrate. When the substrate is deformed by the external force, the resistance value will change, and the bridge will produce the corresponding unbalanced output. The substrate (or diaphragm) used as piezoresistance sensor is mainly silicon wafer and germanium wafer. The silicon piezoresistance sensor made of silicon wafer as sensitive material is paid more and more attention, especially the solid piezoresistance sensor that measures pressure and speed is the most common application.
Application of piezoresistive sensors
Polezoresistive sensors are widely used in aerospace, aviation, navigation, petrochemical industry, power machinery, biomedical engineering, meteorology, geology, seismic measurement and other fields. Pressure is a critical parameter in the aerospace and aviation industries, requiring high accuracy for measurements of both static and dynamic pressure, local pressure, and the entire pressure field. Piezoresistive sensor is the ideal sensor for this aspect. For example, to measure the airflow pressure distribution of the helicopter wing, testing the dynamic distortion of the engine inlet, the pulsating pressure of the grille and the jitter of the wing. In the measurement of the central pressure of the aircraft jet engine, specially designed silicon is usedpressure pickup, Its operating temperature is more than 500℃. The matching silicon pressure sensor with up to 0.05% accuracy is used in Boeing’s atmospheric data measurement system. In the reduced wind tunnel model test, the pressure-resistance sensor can be densely installed at the wind tunnel inlet and in the engine intake duct model.
The single sensor is only 2.36 mm in diameter, the natural frequency is up to 300 kHz, and the nonlinearity and hysteresis are both ± 0.22% of the full range. In biomedical aspects, the piezoresistance sensor is also an ideal detection tool. Injection needle-type piezostatic pressure sensor with diffusion silicon film as thin as 10 microns and only 0.5 mm outer diameter and sensors that measure pressure in cardiovascular, intracranial, urinary, uterine and ocular areas. Figure 3 is a structural diagram of a sensor used to measure cerebral pressure. Piezoresistance sensor is also effectively used in the measurement of explosion pressure and shock wave, vacuum measurement, monitoring and control of the performance of the car engine, such as such as measuring the pressure in the gun chamber, firing shock wave and other weapons. In addition, piezoresistance sensors are widely used in oil well pressure measurement, detection of drilling direction and location of underground sealed cables, as well as flow and liquid level measurement. With the further development of microelectronics technology and computer, the application of piezoresistive sensors will develop rapidly.
What are the typical features of piezoresistive sensors
① The sensitivity coefficient of the piezoresistive sensor is 50-100 times larger than that of the metal-strain pressure sensor. Sometimes the output of the piezoresistive sensor can be measured directly without an amplifier.
② Because it uses the integrated circuit process processing, so the structure size is small, light weight.
③ High pressure resolution, it can detect a small micropressure like blood pressure.
④ The frequency response is good, and it can measure the pulse pressure of several tens of kHz.
⑤ Because the force sensing element and detection element of the sensor are made on the same silicon wafer, it works reliably, with high comprehensive accuracy, and has a long service life.
⑥ Due to the use of semiconductor material silicon production, the sensor is more sensitive to the temperature, if the temperature compensation is not used, its temperature error is large.
Why does the piezoresistive sensor produce a temperature error? How to compensate?
There are two types of piezostatic sensor: one is the adhesive strain gauge made from the body resistance of semiconductor material to form the diffusion resistance made on the substrate of semiconductor material, which is called a diffusion piezostatic sensor.
Piezoresistive sensor is greatly affected by temperature, which will produce zero bit drift and sensitivity drift, resulting in temperature error.
In the piezoresistive sensor, the temperature coefficient of the diffusion resistance is large, and the resistance value changes with the temperature change, which causes the zero drift of the sensor.
The temperature drift of sensor sensitivity is due to the pieoresistance coefficient with temperature. When the temperature increases, the piezoresistance coefficient becomes smaller, and the sensitivity of the sensor is reduced; otherwise, the sensitivity is increased.
Zero temperature drift can be compensated by series and parallel resistance.
The sensitivity temperature drift is compensated by using series diodes in the power circuit of the bridge.
In addition, the piezoresistive sensor can also connect the four diffusion resistance to the whole bridge, in order to reduce the influence of temperature, can use constant current source power supply.
It can be seen that the output of the bridge is proportional to the resistance change, that is, it is proportional to the measured and also proportional to the power supply current. the output voltage is related to the size and accuracy of the constant current source current, but has nothing to do with the temperature, so the constant current source has a good temperature compensation effect.
Disclaimer: This article is reproduced for the purpose of conveying more information. If there is any source labeling error or violation of your legitimate rights and interests, please contact us, we will correct and delete it in time, thank you.